Mobile Laser Cladding for On-Site Machining
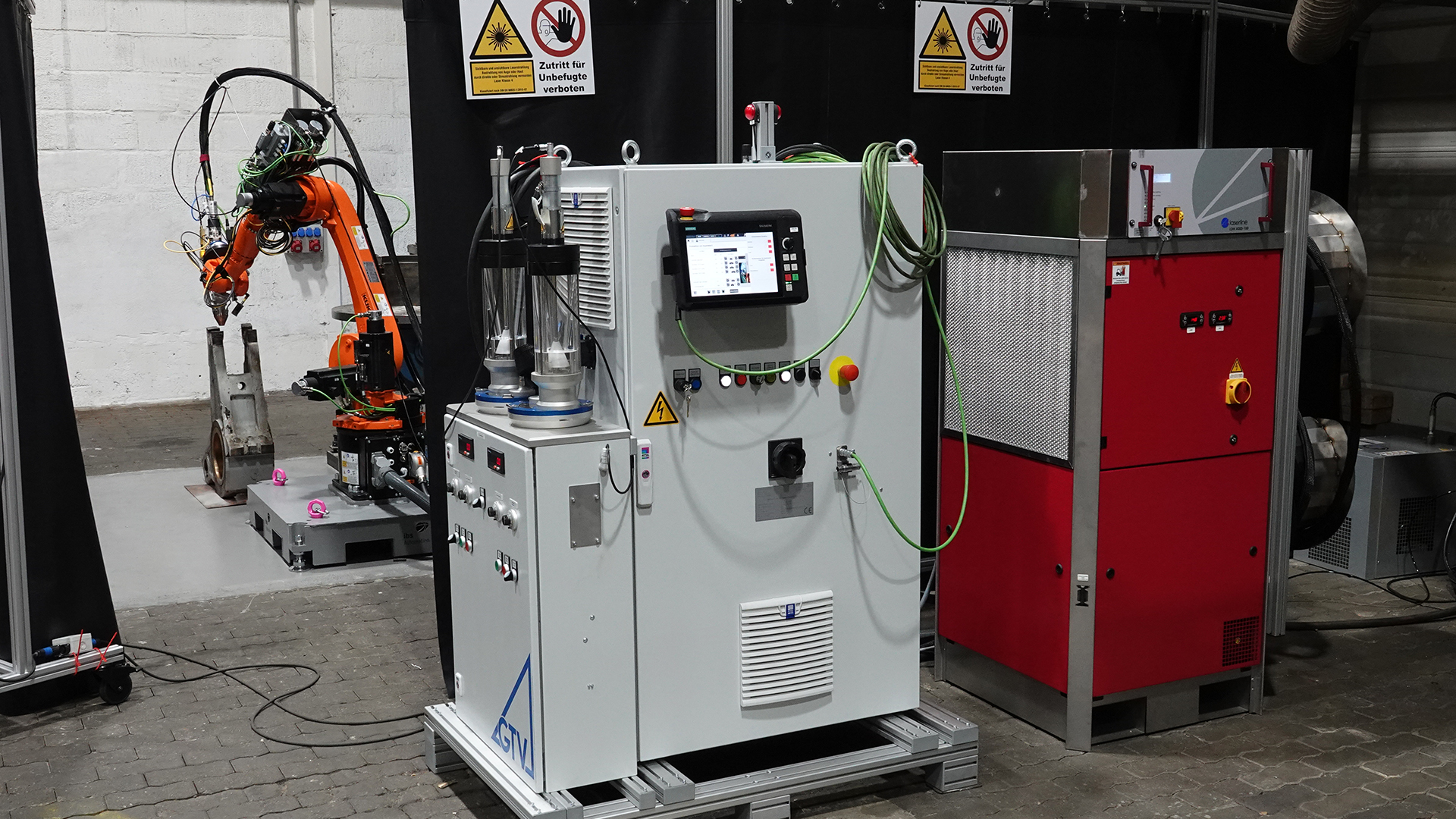
Three practical application examples:
Repair of bearing seats
The bearing seats of both rudders of a cargo ship were damaged and were repaired on site in dry dock. First, the bearing seats were pre-spindled to create a metallically clean and damage-free surface. The surface was then reconditioned to the dimensions of the original contour.
Contact surfaces of a tool holder
The contact surfaces of a tool holder on a hot forging press have exceeded their wear limits and need to be reconditioned. After quickly programming the welding application process in a circular arc, the necessary welding beads are applied layer by layer by the welding robot:
Contact surfaces of bearing caps
The contact surfaces of bearing caps of a marine engine must be repaired in order to restore the seating of the bearings in the caps according to nominal values:
Contact us now
Using our laser cladding you benefit in several ways:
High-precision
processing
Homogeneous
material application
Minimal use
of materials
Cost
savings
Maximum
sustainability
With lots of expertise, passionately inventive and uncompromisingly team-oriented: that's how we are positioned.
With around 200 employees, we are the largest company in the Metalock Engineering Group. Our affiliation with this group ensures that we have worldwide networking and cooperation with experienced specialists from various fields in order to be able to successfully carry out even the most demanding projects. For our assignments, we use machines that we develop in-house, continuously optimize and use exclusively ourselves.
Our clients include corporate groups as well as medium-sized and small companies. How our teams repair the largest machines with a great deal of know-how and highly specialized tools convinces customers from all industries – for example, the automotive, steel, cement, paper and chemical industries, mechanical engineering, energy supply and, of course, shipping. In addition to our technical knowledge and expertise, they appreciate the short reaction times until our specialists are deployed and they are ready to work around the clock.
For more information about Metalock Engineering Germany, please visit: www.metalock.de
Our services
- Mobile machining in industry and marine
- Laser metrology
- Metalock-Repairs
- Laser Cladding and welding repairs
- Machine overhauls
- Mechanical manufacturing
- Damage analysis and assessment
- Strength calculations / FEM analyses
- Reverse Engineering
Our locations in Germany
Contact us now
This is how you use our services:
We will be happy to inform you in advance or help you immediately in case of an emergency. Do not hesitate to contact us. You can reach us via contact form or at lasercladding@metalock.de. In urgent cases, please use our 24-hour emergency assistance number.